Lean construction: How a new paradigm is changing the construction industry
Few industries involve as many different works as the construction industry. This makes clear and binding agreements necessary. However, with projects becoming more complex, it is increasingly difficult to coordinate processes and meet planning specifications. The central aim of the lean approach is to counteract this and guarantee maximum quality, save costs and increase productivity. First used in the automotive industry, the lean approach is now successfully applied by KREBS+KIEFER.
An idea from the automotive industry
In 1990 a book was published in which the term “lean” was coined. In “The Machine That Changed the World”, the American economist James P. Womack describes a particularly successful management system that he had observed and analysed at the Japanese car manufacturer Toyota. He uses the term to describe approaches and methods that enable lean processes and make efficient problem-solving strategies as transparent as possible throughout the value chain. It is a holistic concept that aims to deliver the best possible quality to customers while avoiding unnecessary costs, errors and waste. It is about creating learning organisations that can quickly adapt and respond to changes and challenges. From Lufthansa to Dell to McDonald's, the lean approach has been changing process flows around the world ever since. It has made traditional mass production obsolete, and modern, flexible methods based on the Toyota system have become increasingly established.
Focussing on customer needs
Lean construction (LC) adapts the principles of the lean approach to the construction sector, with the aim of continuously optimising planning and construction processes and always focussing on the needs of the client – highest-quality service at the estimated price within the agreed time frame. When the lean approach talks about waste, it means long waiting times, excessive storage quantities, unnecessary transports and rework. An essential part of improving process stability and avoiding disruptions is harmonised scheduling of trade and work operations. The difference from conventional construction scheduling is essentially that only one trade works in each section or “lot” at a time, and there is maximum transparency in all processes for everyone involved.
Any potential conflicts are immediately visible
When implementing economic objectives, the aim is to plan buildings in a way that makes economic sense throughout their life cycle and beyond. This means we have to consider every phase of a project, from construction and operation to demolition and recycling. We start with the construction costs, include management and modernisation costs and go right through to the cost of demolishing and recycling the building.
The same is true on an environmental level. Can we minimise transport distances for building materials? How can we incorporate local building materials? How do we keep the building’s energy consumption as low as possible? Can we use recycled materials? Can whole structural elements be reused after demolition? What about rubble and other debris? Will it be recyclable? We are constantly finding new answers to all these questions. It’s a challenge that spurs us on to find the best solutions.
We also find answers to sociocultural issues. All our considerations here are aimed at human requirements. We want to plan buildings that focus on people and quality of life. This means protection from cold and heat. It’s also about light, air, noise control and enabling use by as many groups of people as possible.
All these aspects are equally important when planning sustainable buildings. The paradigm shift in the construction industry requires considerable effort on everyone’s part. But it’s an effort that’s worthwhile in every respect.
At KREBS+KIEFER we are convinced of this. We are part of a revolution in the industry. It takes the quality of planning to a new level. Our core competence lies in specialising of different disciplines, which calls for responsibility, creativity and innovation.
Lean construction in international projects
In international construction projects with many different subcontractors, implementing the principles of lean construction is a particularly challenging undertaking, not least due to local differences. KREBS+KIEFER is supported in this by FIDIC, the International Federation of Consulting Engineers. It is the international umbrella organisation of national associations of consulting engineers for construction. FIDIC provides a number of specialised model contracts for international projects, providing a secure basis for sustainable projects executed using lean construction.
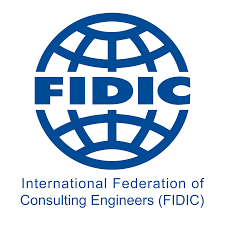
Changing attitudes to break new ground
An example of how well lean construction can be implemented with FIDIC contracts was in spring 2019 during the construction of a motorway in Bosnia and Herzegovina. It was there that KREBS+KIEFER successfully implemented the first LC-compliant pilot project in road construction. The planned lean construction implementation initially caused reservations among many of those involved. The expected transparency, specific commitments and regular performance reviews require trust, not only in one’s own abilities but also in how other companies handle errors. This required a change of attitude from all those involved, which was not easy for everyone at first, and which we had to work hard to encourage. Listening to the concerns of our partners, we were able to promote lean construction at a kick-off meeting, presenting the principles, the potential and the benefits, and putting in hard work to dispel any worries. Ultimately, all the partners began the project with a motivated and positive attitude.
Work that paid off
Our persuasive efforts prior to the pilot project paid off in the end. We showed that lean construction enables projects to be managed in an integrated manner, and executed faster and more efficiently. Above all, we were able to prove that this can be done with the highest quality and within the specified costs and schedule. The success factors were not just the technical expertise of those involved, but also their willingness to be transparent, to take a critical look at processes and to engage in an open, communicative dialogue.
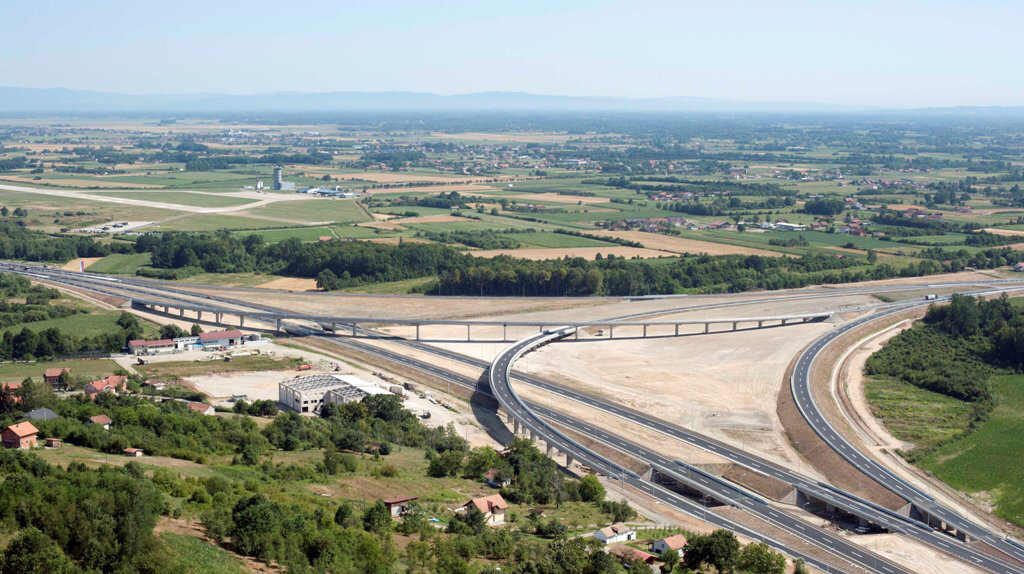